Block for aseptic filling
A protected atmosphere for your product
The Krones aseptic systems family includes experts for all kinds of different sterilisation methods and products to be filled. One of them is the Contipure AseptBloc. Regardless of whether you are blow moulding, filling or capping, with the Contipure AseptBloc every production step is safely included in an aseptic processing chain.
At a glance
- Design:
- Preform sterilisation module
- Aseptic blow moulder
- Aseptic filler and capper
- Suitable for:
- Aseptic filling
- Round, square and rectangular PET containers
- Standard and lightweight containers
- Output: Up to 72,000* containers per hour
- Compact variant: 8,000 to 27,500* containers per hour, for non carbonated beverages
- Only one sterilisation medium: gaseous hydrogen peroxide (H2O2)
* Depending on the container type and product
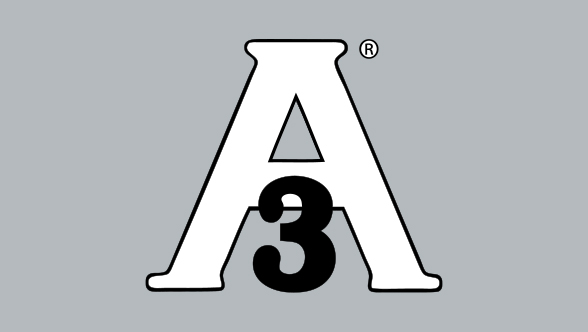
3-A certification for the Contipure AseptBloc
The key components at a glance

Contifeed preform feed system
- Thanks to hygienic design optimal for the Contipure AseptBloc
- Variants adjustable depending on the installation position
Prejet preform rotary rinser
Compact one-starwheel concept at ground level
Method of operation:
- Immersion of the rinser lances in the preforms
- Blowing out of the particles with pre-filtered and ionised sterile air
- At the same time as the particles are blown out: Extraction of the mix of air and dirt
Infrared oven
Servo-controlled oven of the Contiform standard series with efficient and pre-filtered preform air cooling system
Option: Tool-free quick-change of the protective plates of the oven heating mandrels
Optimised in terms of energy:
- Smaller distances between heaters and longer infrared radiators
- Use of parabolic mirrors
Contipure D preform sterilisation module
- The module is between infrared oven and aseptic blowing module.
- Via nozzles, a targeted and directed feed of gaseous hydrogen peroxide (H2O2).
- This provides an overflow and thus results in simultaneous internal and external preform sterilisation.
Aseptic blowing module
- The preforms are transferred to the aseptic blowing module after sterilisation.
- The blowing process takes place within a sterile isolator which is protected from its environment by means of a liquid seal system.
- The stretching rod never leaves the sterile zone during the entire blowing process.
- The blowing process is carried out with pre-filtered sterile air.
Central ventilation technology
Cap sorting and inspection
CapAsept D cap sterilisation module
- Cap blower using ionised air right in front of the unit
- Sterilisation by gaseous H2O2
- No back-up pressure acting on the caps – no deformation
- Clocked feed of the caps on demand: No bottle – no cap
Aseptic capper
- Every capping head has its own separate servo drive.
- A transfer tunnel separates the sterile area from the outside area.
- The proper technique for every cap – overcaps with round bottle possible!
Aseptic filler
Valve manifold
Media module
Benefits to you
Triple protection
The all-round treatment with gaseous H2O2 sterilises the entire preform surface at once: Inside, outside and in the neck area.
Fully-automatic change-over
Handling parts change-over at the filler and the capper can be performed up to a defined output without any manual interference.
Gentle preform treatment
The sterilisation of the preforms hardly leaves any residues: This is because the surface enlarges by many times and the residues of the sterilisation medium are diluted accordingly.
Pinpoint production
Filling to the last drop: The system uses the remaining product quantity in order to calculate exactly how many more PET containers and caps are still to be sterilised.
Proof of safety
The concept of the Contipure AseptBloc has FDA certification and is already in practical use multiple times.
Microbiological safety
The system does not consume any water during operation. Therefore, there is no living space at all for microbiological organisms.
High availability
The entire block is in production for 168 hours non-stop. Depending on the product, it is cleaned and sterilised after 90 minutes or two and a half hours and can be used again. Intermediate cleaning after manual interventions also only takes 30 minutes.
Beverage containers made from rPET
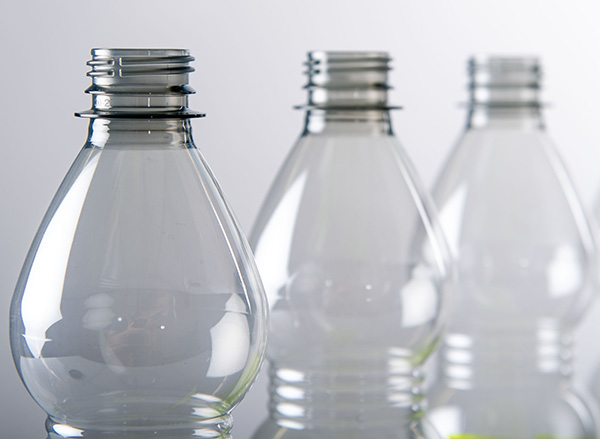
Material properties, processability, food grade quality: you can find all kinds of interesting facts about the use of recycled PET in our free white paper.