Inspection systems Checkmat for fillers and cappers
All-around check for maximum safety and performance
Is the fill level in the bottle okay? Is the cap position straight? Does the tamper-evident ring justify its name? The Checkmat inspection systems give you a clear answer to each of these questions. For example by exactly checking the fill level of the various containers up to within one millimetre and by thoroughly scrutinizing the bottle caps from all sides – regardless whether these are crowns, plastic and aluminium screw caps or tethered caps.
Who is the ideal team partner for the Checkmat inspector? The Krones filler management solutions. They monitor and record important production data providing you with valuable knowledge about the best optimisation.
At a glance
- Fill level inspection unit and missing cap inspection unit
- Fill level inspection unit with high-frequency, gamma or X-ray technology
- Cap and tamper-evident ring detection with sensor and camera technology*, also suitable for tethered caps
- Filler management
- Production management
- Quality management
- Safety management
- Automatic or manual adjustment of the rail as well as the inspection unit height
* Prerequisite: Cap blower for the removal of water drops from the cap and the support ledge.
Benefits to you
- Maximum product quality and safety thanks to continuous container inspection
- Increased line efficiency thanks to automatic detection and rejection of faulty material
Fill level inspection
Technical features
- 1 sensor for underfill and overfill inspection
- Display of analog measured values
- Output: up to 72,000 containers per hour
Range of applications
- Suitable for slightly foaming and non-foaming products
- Not suitable for:
- metallised labels or foiling
- metallised containers
- oils or products containing oil
- beverages with an alcohol content of more than 50 percent
Benefits to you
- No registration rights required
- Operation without any radiation protection officer
Technical features
- 1 camera for underfill and overfill inspection
- Display of analog measured values
- Output: up to 90,000 containers per hour
- Optional with AI for simplified set-up and increased accuracy
(only for glass bottles)
Range of applications
- Suitable for:
- transparent containers
- slightly* foaming and non-foaming products
- label-free zones
- Not suitable for containers with imprints or embossing at fill level height
Benefits to you
- No registration rights required
- Operation without any radiation protection officer
* Clear transition between liquid and foam
Technical features
- 2 sensors for underfill and overfill inspection
- Automatic gamma source shut-off when machine has stopped
- Output of up to 144,000 containers per hour
Range of applications
Suitable for slightly* foaming and non-foaming products
Requirements
- Application requirements
- Radiation protection office
Benefits to you
Suitable for glass and PET containers and cans
* With consistent foaming behaviour
Technical features
- 2 sensors for underfill and overfill inspection
- Output of up to 144,000 containers per hour
Range of applications
Suitable for slightly* foaming and non-foaming products
Requirements
- Application requirements
- Radiation protection officer
Benefits to you
- Precise results – regardless of the product and the label
- Suitable for glass and PET containers and cans
* With consistent foaming behaviour
Technical features
- 2 sensors for underfill and overfill inspection
- Output of up to 144,000 containers per hour
Range of applications
- Suitable for foaming** and non-foaming products
- Suitable for PET containers and cans
Requirements
- Application requirements
- Radiation protection officer
Benefits to you
- Precise results – regardless of the product and the label
- Suitable for glass and PET containers and cans
* Observe country-specific restrictions | ** With consistent foaming behaviour
Cap inspection
Crowns and plastic screw caps
Technical features
- Cost-efficient entry
- 1 unit
- 1 sensor
- Can be integrated in a fill level inspection unit
- Output: up to 90,000 containers per hour
Inspection of the caps for
Presence
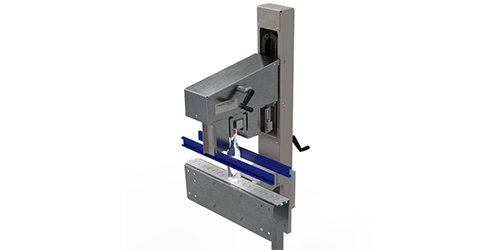
Crowns
Technical features
- 1 unit
- 1 camera with an inspection range of 360° independent
of the rotation position of the print - LED lighting
- Output: up to 90,000 containers per hour
Requirements
No water drops on the caps
iiiiiiiiiiiiiiiiiiiiiiiiiiiiiiiiiiiiiiiiiiiiiiiiiiiiiiiiiiiiiiiiiiiiiiiiiiiiiiiiiiiiiiiiii
Inspection of the caps for
Colour and logo | Correct cap (product mix-up) |
![]() |
![]() |
Position of the printed image | Damaged printed image |
![]() |
![]() |
Plastic screw caps
Technical features
- 1 unit
- 1 compact camera
- Output: up to 90,000 containers per hour
Requirements
Uniform colour
Lateral inspection area inspection of the caps for
Colour
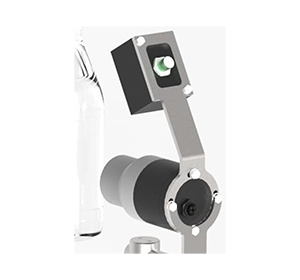
One modular system for all cap types
Technical features
- Compact unit
- 2, 3 or 4 cameras from the side depending of the cap type
- Optional software expansion
- LED lighting
- Output: up to 90,000 containers per hour
Range of applications
- Symmetrical and asymmetrical (tethered) plastic screw caps
- Crowns
- Aluminium roll-on screw caps
- A combination of different types in one product line is possible
Requirements
No water drops* on the caps
* Use of a blower unit required
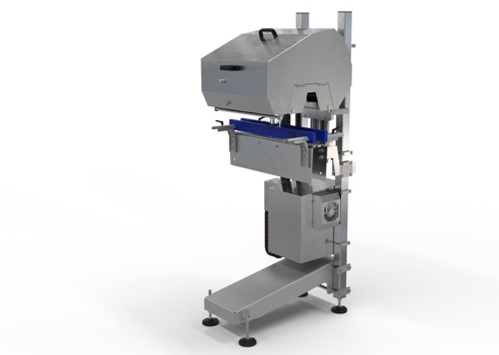