The Krones Group supplied the digital solution as well as the bottling line and the high-bay warehouse. A few years ago, Störtebeker built a new hall on a 40,000-square-metre plot to accommodate the bottling, packaging and logistics kit and opted for digitalization along the entire value chain. “Our aim was to streamline the complex work sequences involved, thus upgrading the production operation’s efficiency,” says Manuel Demske, bottling hall manager at Störtebeker. It was important to ensure full-coverage networking of the system environment, which includes not only Line Management but also systems for managing quality levels, the warehouse and the processes, plus of course SAP’s ERP system. No more jumbled bits of paper, no more typing up notes. That not only avoids errors, it increases efficiency and quality, too.
What’s today’s production schedule? Will we start with Pilsener beer in sixpacks? Or will it be Atlantik-Ale, Bernstein-Weizen (Amber Wheat Beer) or Baltik-Lager in their product-specific crates? Whatever the plan for the day, Line Management, the digital solution from Krones installed at the Störtebeker Braumanufaktur, always knows exactly what’s on the agenda – and controls not only all the machine parameters but also the entire material supply logistics for the line right through to the high-bay warehouse.
Efficient material logistics, optimised bottling processes
Line Management plays a key role in this system because it knows exactly which products are being bottled, how many empties are available, how much bulk glass needs to be fed in, how much product is in the tank, and what further materials are required.
And this is how it works: To begin with, the digital solution controls material supply. An interface to the SAP ERP system automatically provides it with the relevant order data and bills of material, which are checked at the filler and modified as necessary. Once they have been enabled, Line Management sends requests to the warehouse management system for the various materials required, which are made available by six storage and retrieval units. Thanks to Line Management, these units know what is needed in the bottling line. They automatically go up and down the giant shelves in the high-bay warehouse, reliably supplying the bottles, crates and pallets requested, which are taken to the line by an electric ground monorail. “It takes a mere seven minutes to get the materials into the line,” says Manuel Demske. When the pallets have been fully loaded with finished product, Line Management will automatically pass that information to the logistics system which then takes care of moving them into storage.
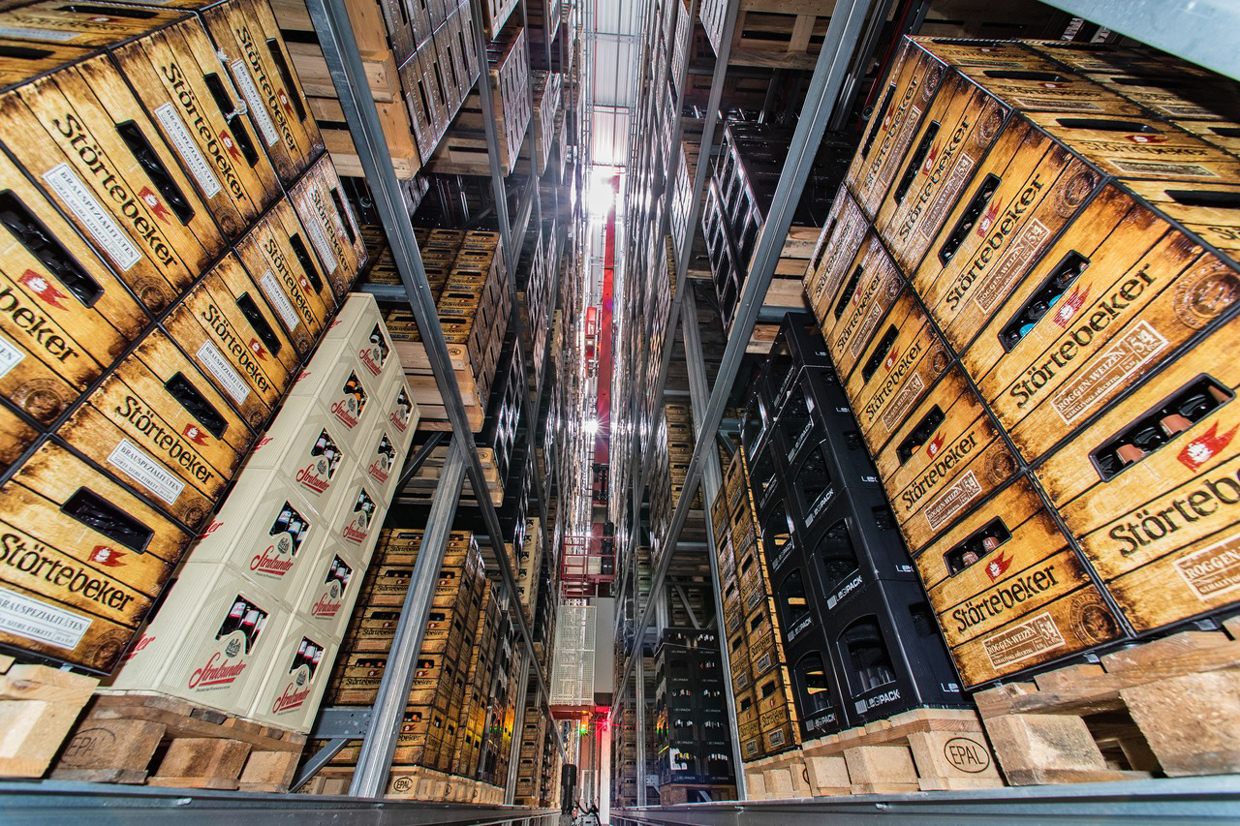
In the line itself, then, Line Management directly matches the machine parameters to the respective orders. That means the machine operators only have to perform the physical changeover of handling parts. The software specifies the path and automatically sets the points – or instructs the operators to do so. Once production is running, the system monitors all production meters in the line, taking due account of any bottles rejected by the inspectors. In this way, the target production quantity is continuously modified as needed, in order to make sure that the planned number of ready-for-dispatch pallets leaves the line. As the order concerned nears completion, Line Management automatically stops infeed of empties and crates. It also makes sure that the machines finish the ongoing order, and that the next product is automatically loaded. “In our bottling hall, product change-overs at the filler take place without any operator intervention whatsoever. Being able to control them automatically – I think that’s simply great. It saves us walking time and as a result filling time, too,” says a gratified Manuel Demske.
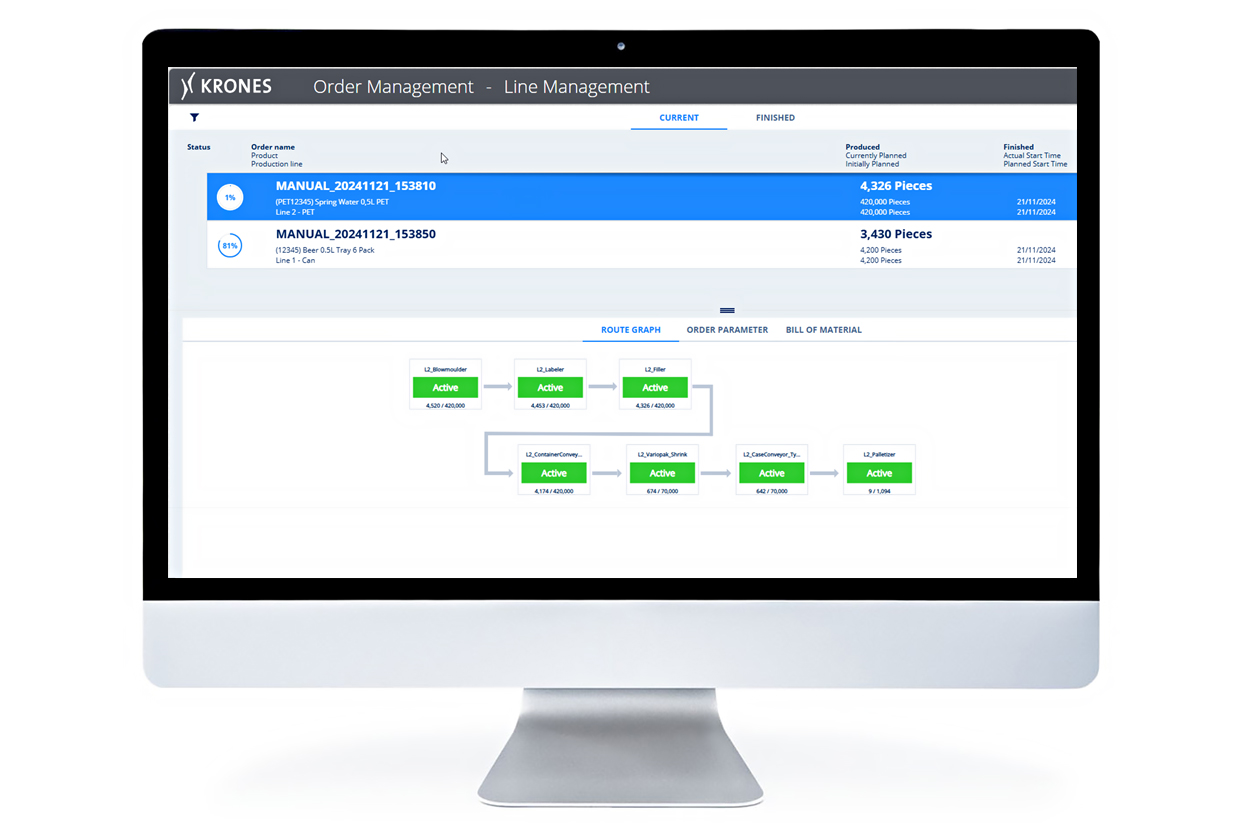
This digital production upgrade significantly reduces the operators’ workload. It is additionally supported by a mobile web app displaying both order status and material consumption. That web app can if necessary be used to request more material and also to generate data for batch tracking, by posting the manually demanded materials directly to the order concerned. “Line Management provides enormous added value for everyone, making their work incredibly easier in very many fields. We’re not just talking bottling here, but also other areas like production planning, logistics and quality assurance,” is how Manuel Demske sums up the benefits.
To increase efficiency even further, Line Management also handles order batching. That means the digital solution sensibly combines the line orders at the individual machines so that these can produce without interruption. Obviously, this will work only if there is no change (like different bottle or label) from one order to the next. This procedure reduces both manual interventions and the number of machine shutdowns and start-ups, which in turn saves time and resources. The software optimises change-overs in such a way that there is no need to empty the line completely. Instead, “a controlled gap” is run along the line, which reliably prevents any intermingling of the two batches. That approach cuts time: The depalletiser at the beginning of the line can already start working on the new order, while the packer at the line’s end is still handling the previous order. Such strategic planning speeds up batch changes.
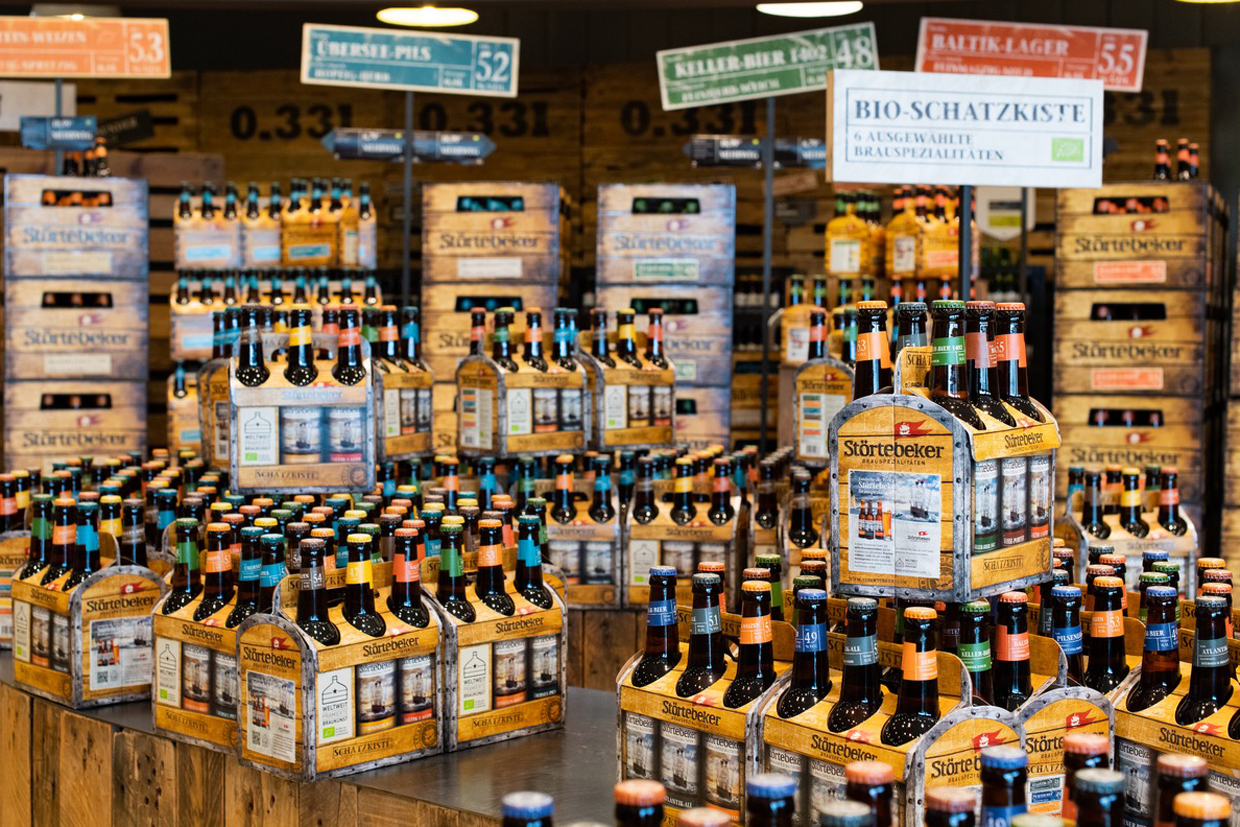
But that’s not all. Line Management also handles the intricate task of crate management, which works as follows: To start with, it passes the empty bottles in returnable crates that enter the line directly to the unpacker, from where they go their separate ways: the returnable bottles towards the bottle washer and then the filler, and the empty crates towards the crate washer. Line Management then makes sure that any clean empty crates leaving the washer that are not needed at the moment are put in storage. As the order nears completion and it comes time to change crate types, Line Management automatically feeds the correct number and type of crates back into the line.
Line Management likewise controls bulk-glass infeed. If too many bottles are rejected by the empty-bottle inspector, it automatically requests the correct number of additional bottles and feeds them into the line, thus preventing any standstills caused by missing bottles. One special feature here is that the application shows the bottle and crate flows in separate displays so that it is easy for the operators to keep a close eye on order-referenced requirements.
And the list goes on: Line Management also controls labelling because bottles, packs, crates and pallets each need their own labels, best-before prints and order-referenced codes. Krones’ smart solution can be relied on to inform printers and coding units of the correct data to be applied in each case. “That substantially reduces human error. For example, it is impossible to order the wrong labels or print the wrong best-before dates. Line Management handles all of that automatically and flawlessly,” says Manuel Demske. And last but not least, Line Management also generates the data for production volumes, material consumption reports and batch tracking and transfers them to the SAP system where just a few clicks suffice to find out which raw materials were used for the finished product on any given pallet.
The solution substantially reduces human error. For example, it is impossible to order the wrong labels. Line Management handles that automatically and flawlessly. Manuel DemskeBottling hall manager at the Störtebeker Braumanufaktur
Always right on course
So, while Line Management takes care of controlling the line, Line Diagnostics is all about monitoring and optimisation, just like a ship’s navigation officer who makes sure the vessel stays on course and bypasses any obstacles. That job starts with creating the requisite transparency. And therefore, Line Diagnostics shows the line’s performance on monitors in the production hall at all times, meaning not just the status of each individual machine but also the condition of the line overall. Are all machines running? Are there any back-ups or even stoppages? That makes sure the machine operators always know exactly how things stand and can swiftly intervene if any problems crop up.
The production managers also have continuous access to information on machine status and can thus monitor and control the process flows involved to optimum effect. Automatic failure analyses help detect any potential malfunctions at an early stage and remedy them in good time. That means Line Diagnostics delivers the information needed to initiate improvements and continuously optimise production processes.
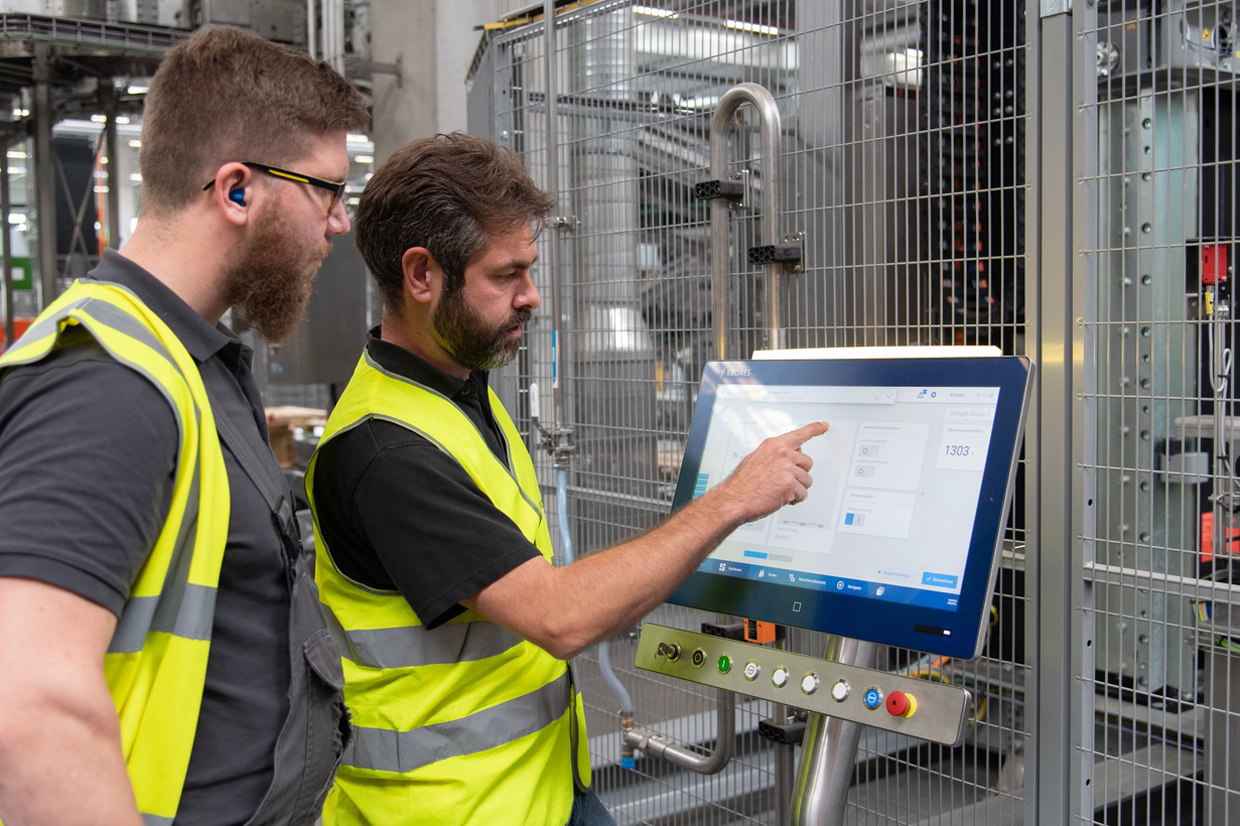
“Working with Krones was excellent,” emphasises Manuel Demske. “They always had an open ear for any subject and suggestions for improvement. These were immediately taken on board and translated into engineered reality.” For example, it was important to the Störtebeker Braumanufaktur that the team planning the modernisation of their IT infrastructure took any previously made investments into due account. And that is precisely what Krones did: The brewery had already been using some SAP systems: ERP, SD for sales and LES for warehouse management. The team of experts from Krones seamlessly integrated these into the new solutions, and also added SAP PP-PI for production planning and SAP MM for material management, thus ensuring smooth operation throughout.
This holistically conceived approach guarantees a high degree of repeatability for the processes concerned and increases both quality and efficiency levels. “The various systems intermesh closely. The huge advantage here is that all processes are automated and completely digital. Especially when certain information like batch data is required, it can be digitally collected ultra-fast, even from home,” says Manuel Demske. This full-coverage digitalization has enabled Störtebeker to admirably meet and master the challenge of handling a large product portfolio, a lot of small batches and many change-overs. And that means: into the future with all sails set.
The various systems intermesh closely. The huge advantage here is that all processes are automated and completely digital. Especially when certain information like batch data is required, it can be digitally collected ultra-fast, even from home. Manuel DemskeBottling hall manager at Störtebeker Braumanufaktur
Why digitalizing production is well worth the effort
- Improving quality and avoiding errors by doing away with manual processes
- Automated control of filling orders, including material supply
- Fewer downtimes and shorter change-over times
- Complete transparency and traceability of processes – from the machine right through to SAP ERP
- Increasing productivity and line efficiency
The Störtebeker Braumanufaktur
The Störtebeker Braumanufaktur can look back on more than 800 years of brewing tradition in the Hanseatic town of Stralsund and has committed itself to brewing a great variety of its own superlatively crafted specialty beers. Each and every one of them is different, and you can see, smell and taste the love and meticulous care that have gone into making them. All of them have gained broad international recognition, not least at the world’s major beer competitions: In recent years, the three specialties Keller-Bier 1402, Roggen-Weizen and Pazifik-Ale were crowned world champions.
After the reunification of Germany, Jürgen Nordmann took over what used to be the Stralsund brewery in 1991 and initiated a strategic refocus – brilliantly. Besides the new name, his concept included particular emphasis on these distinctive specialty beers and on capacity upsizing. At the same time, the brewery invested in a state-of-the-art, energy-efficient bottling line including a high-bay warehouse from Krones. And Störtebeker boldly went one step further: Under its greenfield project, it opted to incorporate digital solutions along the entire value chain. As a result, today it is possible to digitally control all filling processes and material flows.