How can sites be sustainably organised? In mid-May, Dieter Hankofer from Central Field Service answered this question for participants in the “Baustellentag” (Construction Site Day), an event organised by the German Engineering Federation VDMA. As we are sure the topic is also of interest for a wider audience, we have taken the opportunity to look at it in more detail here. And you will find that Krones is tackling the issue from many angles – right in line with its sustainability strategy!
Production lines with Krones equipment are up and running in more than 150 countries all over the world. Of course, when shipping our lines, parts and components, we always choose the route best suited to the particular circumstances involved, striking a healthy balance between swift response times and carbon emission efficiency. And on all its global sites Krones is also strongly focussed on further aspects of sustainability, as the examples in this article vividly demonstrate.
Making full use of digitalization
From North and South America to Europe and Africa right through to Asia: Just like its customers, Krones is represented across the globe with over 100 facilities, which are instrumental in assuring prompt support whenever and wherever a helping hand is needed, “without someone from Germany having to fly over,” says Dieter Hankofer. He adds with a distinct note of pride: “Our local teams are actually able to resolve about two thirds of all service-support requests.”
The benefits of ongoing digitalization don’t stop at service support. They extend to our service colleagues, often enabling them to complete calls without ever travelling to the customer’s site. “Thanks to networked systems and the remote-support option, frequently all our service technicians have to do is log into the line from where they are and take a look at it. Because more often than not, the customer’s staff can get the line up and running again themselves, following the specific instructions given by our colleagues,” says Dieter Hankofer.
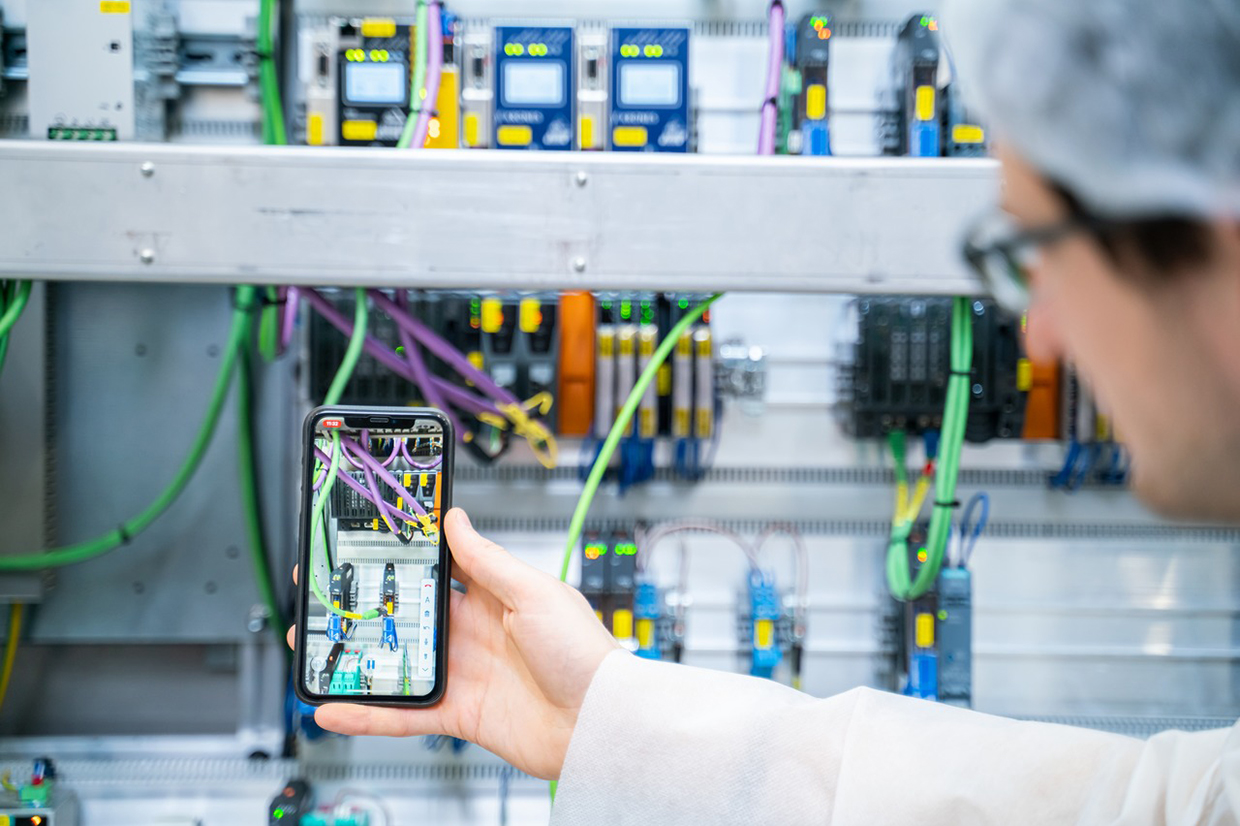
Mind you, it is possible to minimise trips not just for trouble-shooting but for commissioning jobs as well. Dieter Hankofer continues: “The number of commissioning jobs we complete digitally has steadily risen. That means the commissioning team perform their job from Germany by video link. Depending on the complexity involved, they give assistance and/or remotely intervene themselves. Of course, there is always at least one of the local staff present on site.” Some sophisticated planning is required here, especially for commissioning jobs in countries with a big time difference. But that is clearly outweighed by the costs saved for travel and staff. “And in the rare case where virtual commissioning is not successful, you can always still fall back on Plan B: that is, a spontaneous trip to the customer,” adds Hankofer. There has been a marked increase in the number of such smart commissioning jobs over the past few years. “And we obviously want it to grow even further in future,” says Dieter Hankofer.
And if a trip to the customer’s site is unavoidable, Krones will whenever possible choose a sustainable means of transportation. “In Europe and Asia, in particular, but also in the big US cities, e-mobility is a good alternative to conventional internal-combustion vehicles. And that goes for a company’s own vehicles and rented cars alike. It enables us to downsize our carbon emission footprint and helps us move closer to our reduction targets,” says Dieter Hankofer.
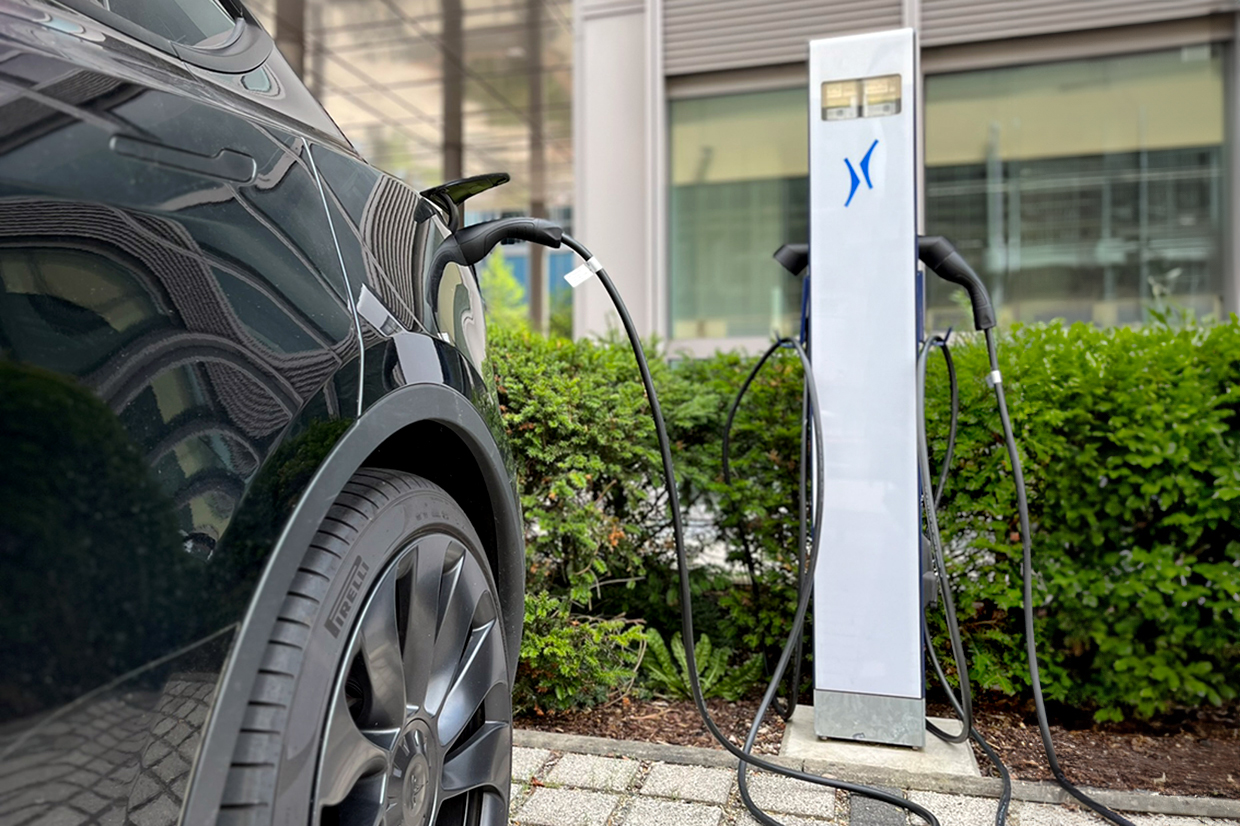
Return any surplus parts and reuse them
Trips planned for people require a fair bit of ingenuity. But even more of that is needed for arranging transportation of our equipment. “In 2023, for example, over 60,000 packages left our German plants alone. That includes shipments of any format and size, ranging from machines proper and entire lines to packages containing a single assembly or various small items,” relates Dieter Hankofer. Obviously, there is plenty of potential for optimisation here. Krones has committed itself to the circular economy concept not only in regard to its products but also in matters of transportation, and translates it into hands-on reality wherever possible.
To start with, we put our dispatch processes under the microscope: “Needless to say, we always go for the most sustainable option,” says Dieter Hankofer. “The packages are usually first transported by lorry or rail, and then taken directly to the customer or to the nearest port for onward transport.” The machines are shipped on large wooden frames, which are reused several times at Krones. Undamaged pallets and crane end carriages are sent back from the sites to Krones’ German plants. “But only if it makes sense in terms of logistics, as it does for a return from sites in Europe, for example,” he adds.
Krones also sends back any surplus parts, such as cables or valves, which are then checked in our plants and stored for further use. “But there are certain restrictions here as well because not every country permits us to simply re-export electronic components, for example,” says Dieter Hankofer. And such returns must, of course, also make logistical sense. For example, those parts which can be checked and stored by our big facilities abroad like our US subsidiary are not returned to Germany. “A few years ago when all sort of parts were in short supply, we were gratified to note that we’re on the right track here, because thanks to this approach, we succeeded in working our way around that scarcity, at least to some extent,” reports Dieter Hankofer.
Recycling precious metals, wood, films & Co.
But Krones also takes back waste proper because some of it offers definite recovery potential, as Dieter Hankofer explains, using leftover cables as an example: “Even the shortest cable end contains valuable copper residues. In our in-house recycling depot at our Neutraubling plant, these are detached, thus producing copper in various quality grades, which enables us to obtain a much better price for resale.” But of course, leftover cables are not the only type of waste from construction sites that is sorted and disposed of by Krones. Based on a clearly structured waste system, wood, films and foils, and paper packaging are disposed of as separate fractions. And of course, the fact that Krones disposes of the waste produced is not only a definite plus for our natural environment, it also means we leave behind a clean construction site.
But although we’d like to, we can’t implement our reuse system in every customer project. Sometimes we come up against regulatory or customs-duty hurdles, and for other shipments the contents quite simply do not justify the transport costs. “However, the fact remains that we do want to tap the still-unused potential and together with our international colleagues are trying to find ways to involve our major centers all round the globe, in particular, even more effectively in this concept,” says Dieter Hankofer. In his view, an overarching cooperation between the teams working on site, in the region concerned and in Neutraubling is of major importance in this context – and above all the courage and determination to bring about change. He believes that “only if we recognize a problem as such and tackle it head-on will we be able to find a sustainable solution.”
Only if we recognize a problem as such and tackle it head-on will we be able to find a sustainable solution.
Dieter HankoferKrones AG